The desuperheater working principle involves injecting atomized cooling water into superheated steam to reduce its temperature to precise, process-safe levels. This prevents equipment damage and optimizes thermal efficiency.
Steam Desuperheater (DSH) Valve
Steam Desuperheater (DSH) Valve is a critical part of the piping system specifically in high Temp Steam applications. uncontrolled high pressure Steam causes significant risks in industrial systems, including turbine blade erosion, pipe stress fractures, and reduced heat exchanger efficiency. Desuperheater valve address these challenges by injecting finely atomized cooling water into steam streams, achieving precise temperature reduction through enthalpy balancing.
Key to steam Desuperheater (DSH) Valve performance is the integration of multi-stage nozzle arrays and dynamic pressure compensation, which ensure uniform water dispersion even at fluctuating flow rates. Advanced designs incorporate PID-controlled actuators and real-time thermal feedback to adapt to load swings in seconds for stem conditioning, preventing overshoot and minimizing thermal fatigue in downstream equipment.
Critical applications of the Desuperheater valve include combined-cycle power plants (attemperation before HRSGs), petrochemical cracking units , and steam-to-water energy transfer. Engineers prioritize pressure reducing desuperheating station (PRDS) models with erosion-resistant trim and self-cleaning nozzles to combat particulate buildup in saturated steam. For compliance with ASME B16.34 standards, modern DSH valves feature integrated strainers and predictive maintenance interfaces that alert to nozzle wear or seal degradation.
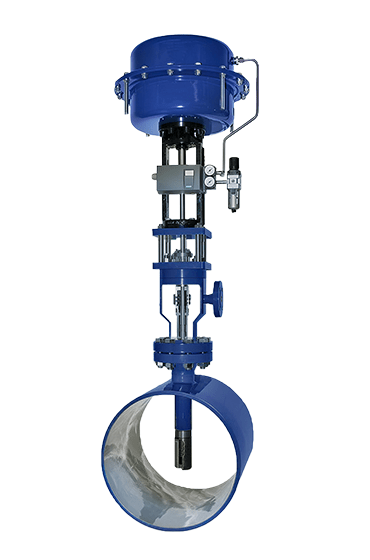
Specifications | Features |
---|---|
Design Standard: ASME B16.34, API 609, ISO 15848-1 (fugitive emissions) Body Material: 316L Stainless Steel, Inconel 625, Duplex Stainless Steel Trim Material: Stellite 6, Tungsten Carbide, Ceramic-coated Operating Pressure: 0.5–200 bar (7–2,900 psi) Temperature Range: -29°C to 600°C (-20°F to 1,112°F) Flow Capacity (Cv): 5–500 (customizable for steam flow rates up to 1,000,000 lb/hr) Turndown Ratio: 50:1 Nozzle Type: Multi-stage, self-cleaning nozzles with anti-clogging geometry Actuation: Pneumatic, Electric, or Hydraulic (PID-controlled for ±1°C accuracy) Response Time: <2 seconds Control Interface: 4–20 mA analog, HART Protocol, or IoT-enabled digital feedback (Modbus, Profibus) Spray Water Particle Size: <50 microns Leakage Class: ANSI/FCI 70-2 Class IV (bubble-tight shutoff) Connection Type: Flanged (ASME B16.5), Welded, or Threaded (NPT, BSP) |
|
FAQ’s
Have a question before you buy our products? Take a look at the FAQs below.
If you don’t find the answer you’re looking for, get in touch with us here.
- What is the primary function of a Desuperheater valve?
- Which industries rely most on desuperheating / attemperation technology?
Power generation, petrochemical refining, HVAC systems, pharmaceuticals, and district heating networks depend on steam conditioning system for critical steam temperature control.
- How do modern DSH valves combat nozzle clogging?
Self-cleaning nozzles, integrated strainers, and ultrasonic anti-fouling coatings minimize particulate buildup, especially in desuperheater handling impure water or saturated steam.
- What happens during rapid load changes?
PID-controlled actuators with real-time thermal feedback adjust water injection within <3 seconds, ensuring stability in pressure reducing desuperheating stations and eliminating temperature overshoot.
- How is thermal shock in downstream piping prevented?
Gradual enthalpy balancing via multi-stage injection in desuperheating systems ensures smooth temperature transitions, avoiding abrupt stress on pipes or turbines.
- How do these systems improve energy efficiency?
By maintaining optimal steam conditions, attemperators reduce boiler fuel consumption by 10–15%, prevent turbine wear, and extend the lifespan of desuperheater heat exchangers.
- How does a desuperheater ensure uniform cooling?
Multi-nozzle arrays and sonic atomization create ultra-fine water droplets, ensuring rapid heat absorption. This process, combined with dynamic pressure compensation, prevents wet steam carryover.
Industries where Steam Desuperheater Valve is Used
Power Generation
Petrochemical Industry
oil and refineries
Chemical Industry
HVAC System
Application
- Heat Recovery Steam Generator (HRSG) Attemperation: Reduces steam temperature before entering turbines to prevent blade erosion and thermal stress.
- Cracked Gas Quenching: Rapidly cools cracked gas streams in ethylene plants to halt reactions and prevent coking
- District Heating Networks: Lowers steam temperature before heat exchangers to prevent thermal shock in residential supply lines
- Bioreactor Heating / Cooling: Balances steam enthalpy for temperature-sensitive fermentation processes.
- Paper Dryer Steam Control: Maintains consistent steam temperature for dryer cylinders to prevent sheet breakage.
- Cleaning-in-Place (CIP) : Delivers exact steam temperatures for sanitization cycles without damaging sensitive equipment.