Plug valves are used to control the flow of fluids in industries like oil and gas, water treatment, and chemical processing.
Plug Valves
We are leading Plug valves manufacturer in Mumbai, India. Plug Valve is a quarter-turn rotary valve designed to regulate the flow of liquids or gases by using a cylindrical or conical plug inside the valve body. The plug rotates within the valve to either allow or block flow, providing a simple and efficient means of fluid control. The valves are widely used in applications requiring tight shut-off and minimal pressure drop
Types of Plug Valves
- Lubricated Plug Valve – These valves use a lubricant, usually injected under pressure, to reduce friction between the plug and the valve body. They are ideal for high-pressure applications and services handling dirty or abrasive fluids.
- Non-Lubricated Plug Valve – Designed without the need for lubrication, these valves rely on polymeric sleevesc or liners to reduce friction. They are commonly used in industries requiring low-maintenance, corrosion-resistant solutions.
- Lined Plug Valve: A Lined Plug Valve is a type of valve with a corrosion-resistant lining, typically made of PTFE or other fluoropolymers, designed to handle aggressive chemicals. It ensures tight shut-off and reliable flow control in highly corrosive process environments.
- Eccentric Plug Valve – This type features an off-center plug, allowing for improved sealing performance and reduced operating torque. It is particularly useful in slurry and wastewater applications.
- Multi-Port Plug Valve –It is a quarter-turn rotary valve designed with three or more ports to facilitate flow diversion, mixing, or isolation within a single valve body. It eliminates the need for multiple valves, reducing piping complexity and installation costs.
Advantages & Disadvantages
Advantages:
- Reliable Shut-off – The valves provide a tight seal, minimizing leakage.
- Quick Operation – The quarter-turn mechanism ensures fast opening and closing.
- Versatile Applications – Suitable for various industries, including chemical, oil & gas, and water treatment.
- Simple Design – Fewer components lead to easier maintenance and installation.
- Bi-directional Flow – Can control flow in both directions, enhancing operational flexibility.
Disadvantages:
- High Torque Requirement – Some designs require significant torque to operate, necessitating actuators or gear mechanisms.
- Potential Wear and Tear – Frequent operation can cause wear on the sealing surface, leading to reduced efficiency.
- Limited Pressure and Temperature Range – Certain plug valves may not perform well under extreme conditions compared to other industrial valves.
Plug valves are essential components in fluid control systems, offering reliable shut-off capabilities, easy operation, and versatile applications. Whether in the oil and gas sector, water treatment, or chemical processing, their simple design and robust performance make them a preferred choice for many industries. Selecting the right plug valve depends on factors such as pressure rating, material compatibility, and operational environment to ensure optimal performance and longevity.
Key Features
- Material Options: Available in stainless steel, carbon steel, ductile iron, and various alloys for compatibility with different media.
- Sealing Mechanism: Includes metal-to-metal or soft-seated designs to accommodate different operational needs.
- Flow Control: Provides excellent throttling capabilities in specific applications.
- Pressure Ratings: Typically designed for medium to high-pressure applications, with variations based on industry requirements.
- Compact Design: Space-saving structure with a minimal footprint, making installation easier in confined areas.
Why Freture Techno?
As trusted Plug Valve Suppliers in India, we offer a wide range of valves suitable for chemical processing, oil & gas, and water treatment applications. With a strong global presence as reliable Plug Valve Exporters in India, Freture Techno ensures each valve meets international standards, offering exceptional performance, corrosion resistance, and long service life across demanding industrial environments.
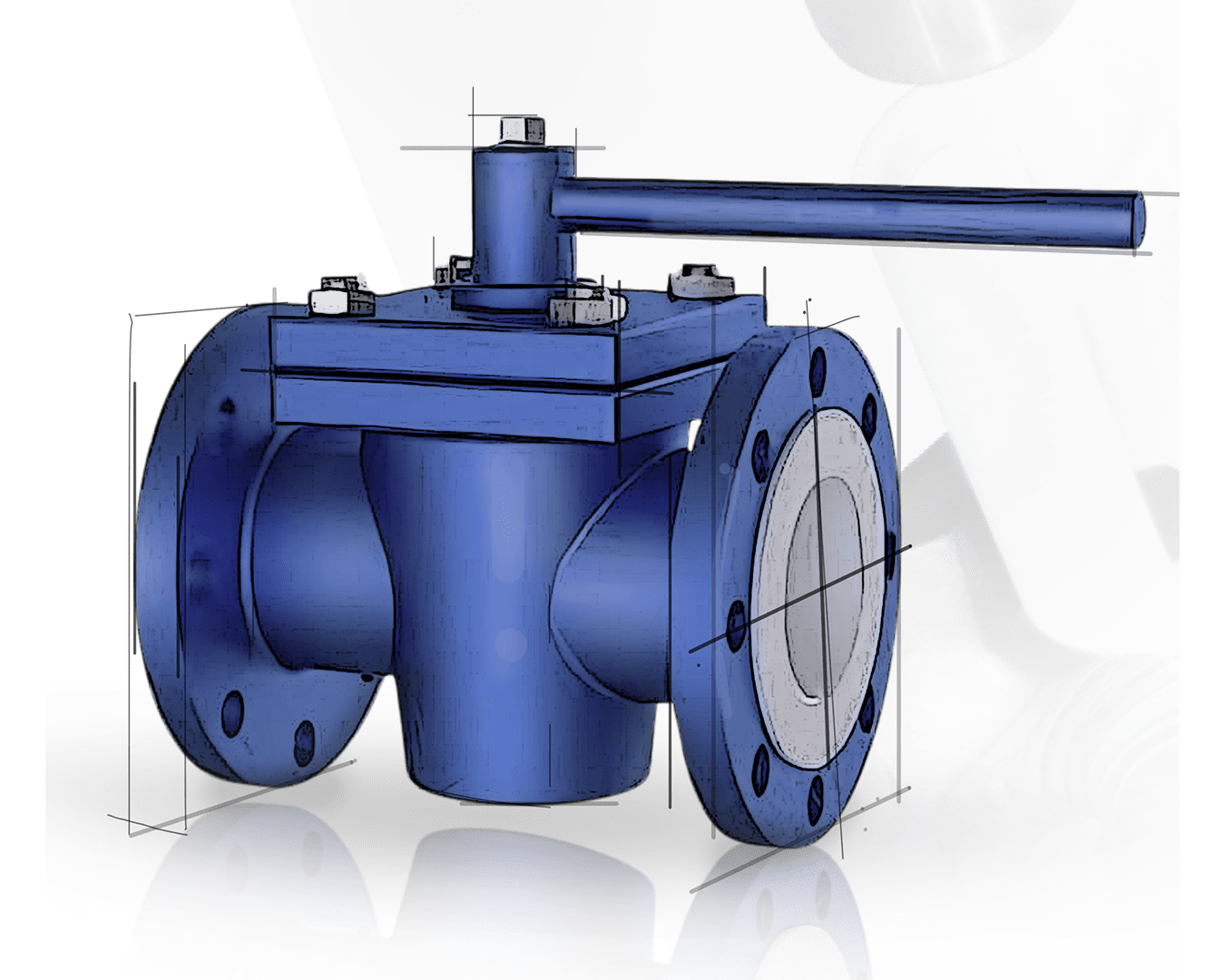
FAQ’s
Have a question before you buy our products? Take a look at the FAQs below.
If you don’t find the answer you’re looking for, get in touch with us here.
- What is a plug valve used for?
- How does a plug valve work?
A plug valve operates by rotating a cylindrical or conical plug within the valve body to open or close the flow passage.
- What are the main types of plug valves?
The main types include lubricated, non-lubricated, eccentric, and expanding plug valves.
- What are the advantages of using a plug valve?
Advantages include reliable shut-off, quick operation, simple design, and bi-directional flow control.
- Where are plug valves commonly used?
They are used in industries such as oil and gas, water treatment, chemical processing, and power generation.
- What materials are plug valves made from?
They can be made from stainless steel, carbon steel, ductile iron, and various alloys.
- How do lubricated and non-lubricated plug valves differ?
Lubricated plug valves require lubrication for smooth operation, whereas non-lubricated plug valves use polymeric sleeves to reduce friction.
- Are plug valves suitable for high-pressure applications?
Yes, certain plug valves, especially lubricated ones, are designed for high-pressure applications.
- What are the disadvantages of plug valves?
Some disadvantages include high torque requirements, potential wear and tear, and limited performance under extreme conditions.
- How can I select the right plug valve for my application?
Selection depends on factors like pressure rating, material compatibility, sealing mechanism, and operational environment.
Industries where Plug Valve is Used
Chemical Processing
Pharmacutical Industry
Power Generation
Oil and Gas Industry
Water Treatment
Applictaions
- Oil and Gas Pipelines – For quick shutoff and reliable sealing.
- Chemical Processing Plants – To handle corrosive and viscous fluids.
- Water Treatment Systems – For flow control in high-purity systems.
- Pharmaceutical Industry – In sterile, clean-in-place (CIP) environments.
- Power Generation – For high-pressure and high-temperature service.